Post Tension Cables Spacing: How Far Apart and How Deep To Install
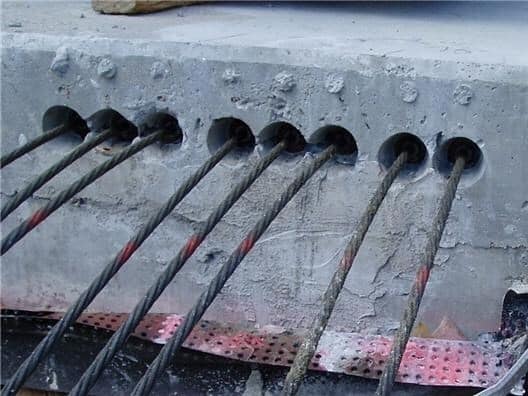
Post-tensioning is a technique widely used in construction to reinforce concrete structures. It involves the use of post-tension cables, which are tensioned after the concrete has been poured. These cables add strength and durability to the concrete, making it capable of withstanding greater loads and reducing the risk of cracking or failure.
One critical aspect of post-tensioning is determining the spacing and depth at which the cables should be installed. In this article, we will explore the factors that influence post tension cable spacing and depth and provide guidelines for their optimal installation.
Understanding Post-Tension Cables
In the realm of construction and engineering, there are various techniques and materials that help strengthen structures and enhance their durability. One such innovation is the use of post tension cables.
Post tensioning is a method that involves applying tension to steel cables or bars, commonly known as post tension cables, to counteract the forces that a structure may encounter over time. They are typically tensioned after the concrete has been poured, applying compressive forces to the concrete and enhancing its load-bearing capacity.
By introducing post-tension cables, engineers can create more efficient and structurally sound buildings, bridges, and other structures. These cables are used in a wide range of construction projects, from bridges and buildings to parking structures and stadiums.
Factors Influencing Post Tension Cables Spacing
Several factors come into play when determining the spacing of post-tension cables. These factors are essential to ensuring the structural integrity of the concrete. Let’s take a look at some of the key considerations:
- Load and Structural Design: The primary purpose of post-tensioning is to reinforce the concrete structure to bear specific loads. The spacing of the post-tension cables depends on the design loads and the structural requirements of the project. A structural engineer will perform calculations to determine the appropriate spacing for the cables based on the anticipated loads.
- Concrete Strength and Thickness: The strength and thickness of the concrete slab or member also influence the spacing of post-tension cables. Thicker and stronger concrete may require fewer cables and wider spacing, while thinner or weaker concrete may necessitate closer spacing of cables.
- Cable Diameter and Tensile Strength: The diameter and tensile strength of the post-tension cables themselves play a crucial role in determining the spacing. Cables with larger diameters and higher tensile strengths can span longer distances between anchorage points, allowing for wider spacing.
- Crack Control: Another factor to consider is crack control. Post-tensioning helps control cracking in concrete, and the spacing of the cables affects this control. Closer spacing can help limit crack widths, especially in areas where cracking is more likely to occur.
- Construction Sequence and Formwork: The construction sequence and formwork used during the concrete placement are also factors to consider. If the formwork is not adequately supported, closer cable spacing may be necessary to prevent deflection or sagging of the formwork.
Guidelines for Post Tension Cables Spacing
While the exact spacing requirements for post-tension cables vary depending on the factors mentioned above, there are some general guidelines to follow. These guidelines provide a starting point for determining the appropriate spacing:
- For slabs and beams, a common rule of thumb is to maintain a minimum spacing between cables equal to the slab thickness, with a maximum spacing of 3 feet (0.9 meters).
- The closer spacing (closer to the slab thickness) is typically used in areas where cracking is a concern, such as corners, edges, or regions subjected to high tensile stresses.
- For post-tensioned columns or walls, the spacing will depend on the structural design and loading conditions. It is essential to consult a structural engineer to determine the optimal spacing in these cases.
- It’s important to note that these guidelines are not universal and should be customized based on the specific project requirements and structural calculations.
Determining Post Tension Cables Depth
The depth at which post-tension cables are installed is equally important to ensure their effectiveness in reinforcing the concrete structure. Here are some considerations for determining the appropriate depth:
- Cover Requirements: The depth of the cables should comply with the cover requirements specified by the design standards and codes. The cover refers to the distance between the outer surface of the concrete and the nearest surface of the tensioning cables. Adequate cover is necessary to protect the cables from corrosion and external elements that may compromise their performance and longevity.
- Concrete Durability: The depth of post-tension cables also affects the durability of the concrete. Placing the cables too close to the surface can increase the risk of corrosion due to exposure to moisture, chemicals, or environmental factors. On the other hand, placing them too deep may reduce their effectiveness in reinforcing the concrete.
- Construction Considerations: The construction process and site conditions can influence the depth of post-tension cables. Factors such as available space, access for installation, and coordination with other building systems may dictate the maximum allowable depth.
- Anchorages and Stressing Requirements: The anchorages and stressing requirements also have an impact on the depth of post-tension cables. The cables need sufficient length within the concrete member to be effectively anchored and stressed. The depth should accommodate the necessary length while maintaining proper cover requirements.
Guidelines for Post Tension Cables Depth
While specific depth requirements will vary based on project specifications, industry standards, and design calculations, here are some general guidelines to consider:
- For slabs and beams, a common recommendation is to place the cables at a depth of at least 1.5 inches (38 mm) below the top surface of the concrete. This ensures adequate cover and protects the cables from potential damage during construction and use.
- In areas where environmental conditions or corrosive agents are a concern, a greater depth may be necessary to enhance the durability of the cables. Consult the design standards and recommendations specific to the project location.
- It’s crucial to coordinate with the project’s structural engineer and adhere to the design drawings and specifications. The engineer will provide detailed calculations and recommendations regarding the optimal depth for the post-tension cables.
Installation Techniques for Post-Tension Cables
Proper installation techniques are crucial to ensuring the effectiveness and longevity of post-tension cables. The following steps outline the general installation process:
- Preparing the Construction Site: Before installing post-tension cables, the construction site must be properly prepared. This involves ensuring the formwork and reinforcement are in place, and any necessary anchorages or ducts are correctly positioned.
- Step-by-Step Cable Installation: The installation process typically involves the following steps:
- Placing the ducts or sheaths: Ducts or sheaths are placed in the desired locations where the post-tension cables will be installed.
- Inserting the cables: The post-tension cables are threaded through the ducts or sheaths, ensuring they are properly aligned and positioned.
- Anchoring the cables: The cables are securely anchored at the ends of the structure, using specialized anchorages designed for post-tension systems.
- Tensioning the cables: After the concrete has sufficiently cured, the cables are tensioned to the specified forces using hydraulic jacks.
- Grouting the ducts: Once the cables are tensioned, the ducts are grouted to provide protection and ensure the cables remain in position.
- Quality Control Measures and Inspections: Throughout the installation process, it is essential to perform quality control measures and inspections. This includes checking the alignment and positioning of the cables, verifying the proper tensioning force, and conducting comprehensive testing to ensure the cables meet the specified requirements.
Summary
Determining the spacing and depth of post-tension cables is crucial for ensuring the structural integrity and longevity of concrete structures. Factors such as load requirements, concrete strength, crack control, and construction considerations all influence the spacing decisions. Similarly, cover requirements, concrete durability, anchorages, and stressing requirements affect the depth of the cables.
While there are general guidelines available, it is essential to consult with a structural engineer or design professional for specific project requirements. Their expertise and calculations will provide the most accurate and reliable recommendations tailored to the project’s unique needs.
By following these guidelines and working closely with professionals, you can ensure the proper installation and effectiveness of post-tension cables in reinforcing your concrete structures, leading to safer and more durable construction.
FAQs
What are the typical materials used for post-tension cables?
Post-tension cables are typically made of high-strength steel strands or tendons.
Can post-tension cables be retrofitted into existing structures?
Yes, post-tension cables can be retrofitted into existing structures to enhance their load-bearing capacity or address structural deficiencies.
Are there specific building codes and regulations governing post-tension cable installation?
Yes, building codes and regulations vary by jurisdiction, and it is important to comply with local codes and regulations when installing post-tension cables.
How do post-tension cables compare to traditional reinforcement methods?
Post-tension cables offer advantages such as increased strength, reduced material usage, and improved structural efficiency compared to traditional reinforcement methods.
What are the common signs of post-tension cable failure or distress?
Signs of post-tension cable failure or distress may include excessive cracking, sagging, deflection, corrosion, or unusual noises.
Is it possible to adjust the spacing and depth of post-tension cables after installation?
Generally, it is not recommended to adjust the spacing and depth of post-tension cables after installation, as it can compromise the structural integrity of the system.
How long do post-tension cables typically last before requiring replacement or maintenance?
The lifespan of post-tension cables can vary depending on several factors, including the quality of materials used, environmental conditions, and maintenance practices. However, with proper installation and regular maintenance, post-tension cables can last for several decades before requiring replacement. It is important to conduct periodic inspections, monitor stress levels, and address any signs of distress or damage to ensure the long-term performance and durability of the post-tension cable system. Engaging with structural engineers and following recommended maintenance practices will help extend the lifespan of post-tension cables and maintain the structural integrity of the construction project.