Ready Mix Concrete vs. DIY Mixing: Which One Is More Cost-Effective?
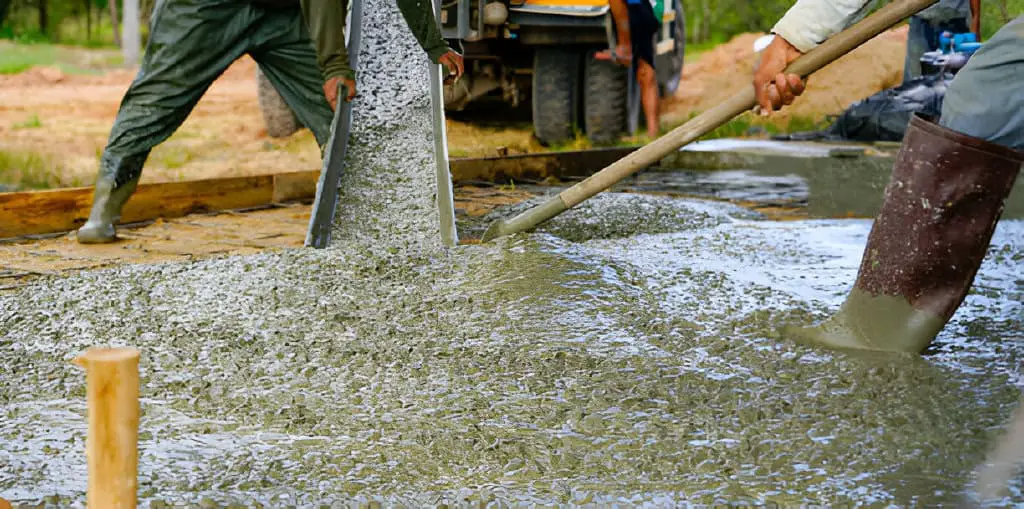
When starting a construction project, like a new driveway or patio, you’ll need to choose between ready-mix concrete and mixing it yourself. Both options have their pros and cons, but which one truly offers the best bang for your buck?
I’ve tackled this dilemma myself, and I’ve come away with some valuable insights. Let’s dive into the nitty-gritty of ready mix concrete versus DIY mixing to find out which is more cost-effective.
The Basics: What’s the Difference?
Before we get into the numbers, let’s break down what each option entails. Ready mix concrete comes pre-mixed from the supplier, delivered right to your site, and ready for pouring. Think of it like ordering a fully cooked meal from a restaurant—convenient and hassle-free.
On the other hand, DIY mixing involves buying the raw ingredients—cement, sand, gravel, and water—and mixing them yourself. This is akin to cooking from scratch at home; it requires more effort but can be more customizable.
The Cost Factor: Ready Mix Concrete
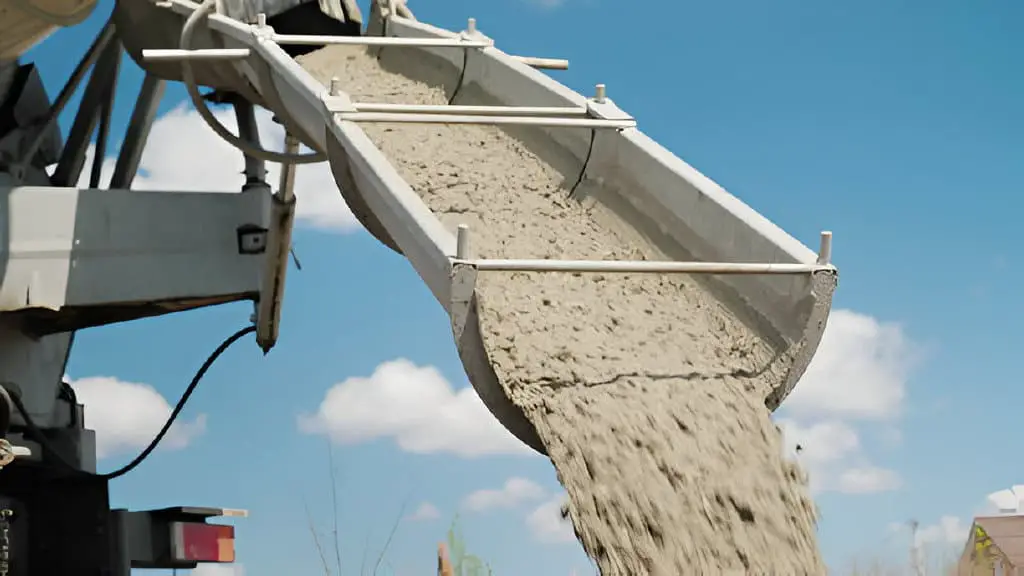
For cost analysis, we must break down the material costs. This will show which is cheaper: ready mix or DIY mixing.
Besides raw materials, transportation costs for bulk supplies are often overlooked. When choosing ready mix concrete, suppliers usually charge for delivery. The fee depends on the distance and the order size.
Ready mix concrete promises convenience and consistency, but it often comes with a heftier price tag. The cost includes not just the materials but also delivery fees and potential minimum order quantities. Here’s a rough breakdown of what you might expect:
Expense | Estimated Cost |
Concrete (per cubic yard) | $100 – $150 |
Delivery Fee | $75 – $150 |
Minimum Order Quantity | 3 – 4 cubic yards |
Why the Higher Price?
- Convenience: You get a ready-to-use product without the sweat and tears of mixing.
- Consistency: The concrete mix is perfectly balanced for strength and durability.
- Time: Less labor means you can get your project done faster.
Also check out: How Long Does Reinforced Concrete Last?
The Cost Factor: DIY Mixing
Mixing concrete yourself can be an appealing option if you’re looking to save some cash. Here’s what you’ll need to budget for:
Expense | Estimated Cost |
Cement (per bag) | $10 – $15 |
Sand (per cubic yard) | $30 – $50 |
Gravel (per cubic yard) | $30 – $50 |
Water | Minimal cost |
Equipment Rental | $50 – $100 |
Why the Lower Price?
- Raw Materials: Purchasing individual components can be cheaper than buying a pre-mixed product.
- Flexibility: You can mix only what you need, reducing waste.
Hidden Costs and Considerations
- Labor and Time: Mixing concrete by hand or even with a small mixer is labor-intensive. It takes time, and there’s a learning curve.
- Quality Control: Without proper knowledge, achieving the right mix can be challenging. Improperly mixed concrete can lead to weaker results and future repairs.
- Tools and Equipment: You’ll need additional equipment like a concrete mixer or wheelbarrow, which can add to the cost.
Pros and Cons: A Closer Look
Ready Mix Concrete
Pros:
- Consistent Quality: Perfectly mixed for durability.
- Less Labor: Minimal effort required on your part.
- Time-Saving: Faster completion of your project.
Cons:
- Higher Cost: More expensive due to convenience and delivery.
- Minimum Orders: You may have to order more than you need.
DIY Mixing
Pros:
- Cost-Effective: Generally cheaper, especially for small projects.
- Customizable: Adjust the mix as needed for different applications.
Cons:
- Labor-Intensive: Requires significant physical effort.
- Quality Risk: Potential for inconsistency and weaker concrete.
- Time-Consuming: More time needed for mixing and preparation.
Read: Green Concrete vs. Traditional Normal Concrete: What’s the Difference?
Project Efficiency: Impact of Project Scale on Cost-Effectiveness
When it comes to the cost-effectiveness of ready mix concrete versus DIY mixing, one crucial factor to consider is the scale of your project. Small-scale renovations often favor a cheaper, more flexible approach. Mixing concrete on-site can be a good option for this.
For these small projects, controlling the mix design is key. Adjusting quantities as needed, without wasting leftover materials, can cut costs.
However, with larger projects, like building foundations or commercial structures, the dynamics change. Here, time is money in its most literal sense. Using ready mix concrete can be more efficient than manual mixing at this scale. It has precise formulations and is delivered directly to your site.
The reduced labor hours spent on batching and testing mixes onsite. This streamlines operations and speeds up project completion. It may save money by cutting overhead and avoiding delays.
Read: How to Increase the Height of an Existing Concrete Slab?
My Personal Experience
I’ve gone both routes in different projects. For a small garden wall, I opted for DIY mixing to keep costs down. The process was laborious, and I ended up with a few too many bags of cement and some questionable mixes. The wall turned out fine, but the experience taught me that DIY mixing isn’t always as straightforward as it seems.
On the other hand, when I built a larger patio, I chose ready mix concrete. The convenience was unmatched—no mixing or measuring, just pouring and smoothing. The consistency was spot-on, and the patio has held up beautifully over the years. The extra cost was worth it for the peace of mind and professional results.
Conclusion: Making the Right Choice
When choosing between ready mix concrete and DIY mixing, consider your project’s size, budget, and your comfort with mixing. Ready mix concrete is convenient and of high quality. So, it’s ideal for large or precise projects. DIY mixing can save money, especially for smaller tasks, but it demands more time and effort.
In the end, both options have their place in the world of concrete. By weighing the costs and benefits, you can make an informed decision that fits your needs and ensures the success of your project. So, roll up your sleeves or place that order—either way, you’re one step closer to achieving your concrete goals.